
THE STRONGEST ARGUMENT FOR THE BX
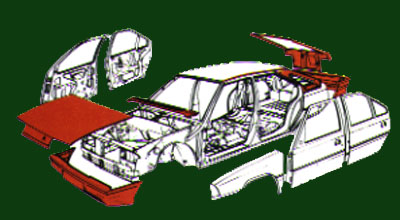
The BX includes comprehensive anti-corrosion protection. Naturally, the polymer body components and bumpers cannot corrode- but, in addition, much of the structure includes special steels whose low carbon content makes them less prone to rust. Zinc coated steels, cataphoretic zinc coating, waxing of box sections and flexible sealants amply protect other vulnerable points. Moulded liners help prevent stone chips under the wheel arches.
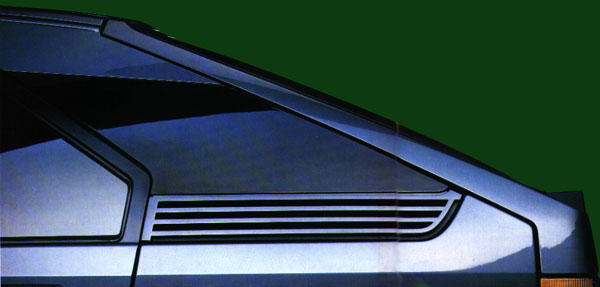
The BX bodyshell includes special high-strength steels with a better strength to weight ratio. It was the first full production car with modern synthetic materials for large non-structural panels such as the bonnet lid and the tailgate - even the window glass is slightly lighter and, being bonded to the bodyshell, helps improve the strength to weight ratio. It all adds up to major savings in weight which, when coupled to modern all alloy engines, produces responsive acceleration, greater fuel economy and safer stopping. The BX is also the product of one of the most modern assembly lines in Europe. The widespread use of robot welding equipment and computer controlled production lines in both body and engine plants ensures consistent quality.
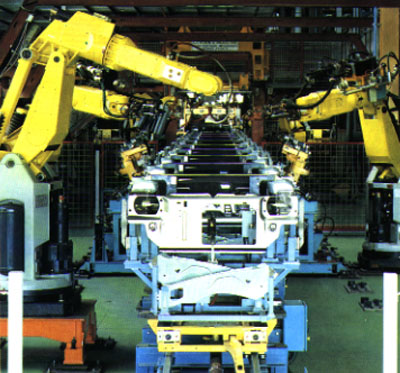
ROBOTS HELP TAKE THE WORK OUT OF OWNING A BX
This has a number of practical benefits- for instance computerised engine testing means that; unlike some competitors, the BX diesels do not require subsequent head bolt tightening.
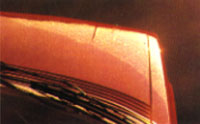
The BX's bonded windscreen saves weight, increases the rigidity of the structure and reduces wind drag. Single large wiper cuts drag and lifts less at speed. Rear screen is bonded too.
DESIGNED FOR SIMPLE, LOW COST SERVICING
All round, the BX's advanced design and manufacture offers savings on the cost of ownership. Self-adjusting clutch and brakes reduce routine servicing - though further savings are achieved by thoughtful design. For example, brake discs can be replaced without dismantling the hubs - they come off and re-mount almost as easily and quickly as changing a wheel. The self-levelling suspension system eliminates the need for routine shock-absorber replacement - and the entire suspension system can be serviced without recourse to special tools. On models not including the new sealed-for-life gearbox, the unit is easily accessible without lifting out the engine, and the clutch can be changed more quickly thanks to an access panel within the wheel arch. If you're on the road and a fuse or bulb blows you'll find the fusebox within the car, under the dash - and the head and tail light clusters can be removed without tools. On average a BX shouldn't require more than two and a half hours routine servicing annually.
EFFECTIVE PROTECTION AGAINST CORROSION
The steps to combat rust start with painstakingly selected metals being given a special anti-corrosion treatment. Next, the body is washed, de-greased and bonded with a zinc phosphate inhibitor that's baked on at 180°C. Then the car is immersed totally in a cataphoretic bath that uses electric polarity to coat every part of the bodyshell with a protective resin. Further preventatives include wax injections into the box sections of the framework, and bitumen painting of the underbody and vulnerable wing sections. An electrostatic primer and two coats of paint are finally baked on at high temperature to give a. tough, high gloss finish - one that will last for many years.
ENSURING THE HIGHEST STANDARDS OF QUALITY CONTROL
Citroen have extended the concept of quality control by involving those best qualified to maintain standards. The work force. Throughout the plant special inspection areas have been set up. Here, at each stage of the process, the different parts of the car are examined by those who work on them. In addition to writing their comments, they are in the position to implement the findings. All of which results in a far more effective system of controlling quality.
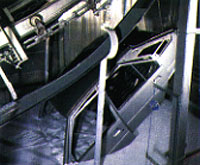